-Hertz and Tunes
5th of June 2018
Electricity is plain incredible. The more I explore it, the more I am sure we're just at the tip of its iceberg. The past 3 weeks I've been exploring how to generate magnetic fields using coils and modulated electric pulses. Not only that, but to generate them in a certain frequency. Not only that, but to have these frequencies in tune with eachother. Not only that, but more.
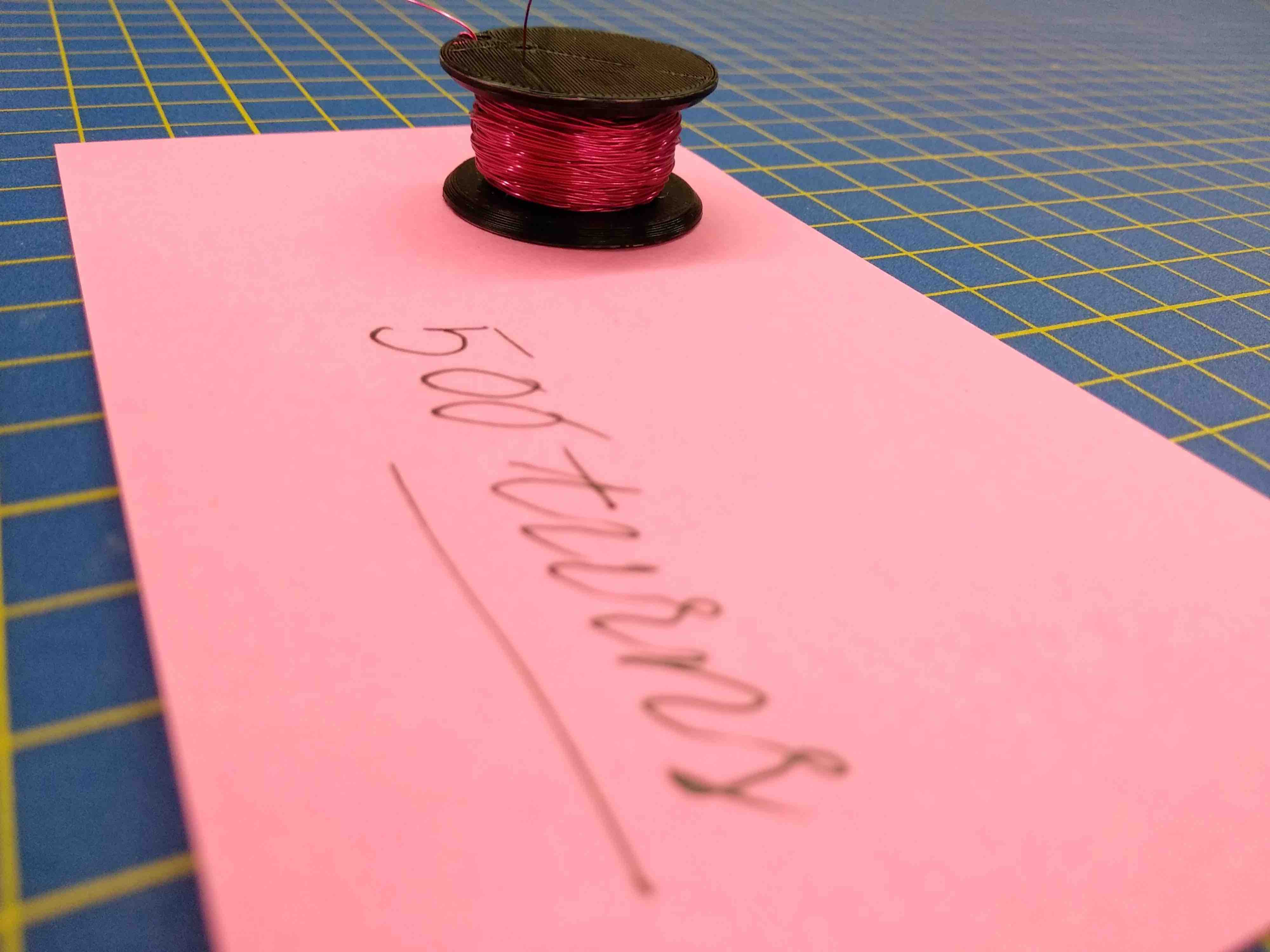
Work in a fab-lab and having access to digital fabrication tools get you to do almost anything, really (the original name of our current Fab Academy is still a great name, and simply because it says what is does). Designing and 3D Printing a structure for the copper wire (30 Gauge) took me 30 minutes. Today was the first test, running the coils at 32Hz, a C tune; 38Hz, a D tune; 40Hz, an E tune;
And why am I so thrilled about it? -Well, everything has a frequency. I reckon I've just started tapping potentiously an ocean of discoveries.
One of the experiments I ran today was to make a Neodymium magnet oscillate at the system's frequency. Unexplainable the sensation to have the power to control that.
These experiments are in conjuction with my Augusto Weber, Doctor, musician and Acupuncturist. He wrote a book about the healing powers of music.
6th of June
While researching about Decoupling Capacitors to add to the documentation of the Bueno Board 32U4 under Bypass Cap, I came accross some interesting characteristics of ceramic capacitors, that is pertinent to this post.
Ceramic capacitors are made out of various thin layers of a special piezo ceramic and because they're made out of Piezo crystal material, it is possible to "play" a ceramic capacitor, as you would do it with a piezo speaker or a common loudspeaker.
This input might become a whole topic for a future post.
I keep you posted.
-Chips of Wax Blocks
3rd of April 2018
To comprehend how to make a pre-mold of a mold of the part you want casted, feels sometimes like a twister game - but instead of twisted arms and legs, your brain!
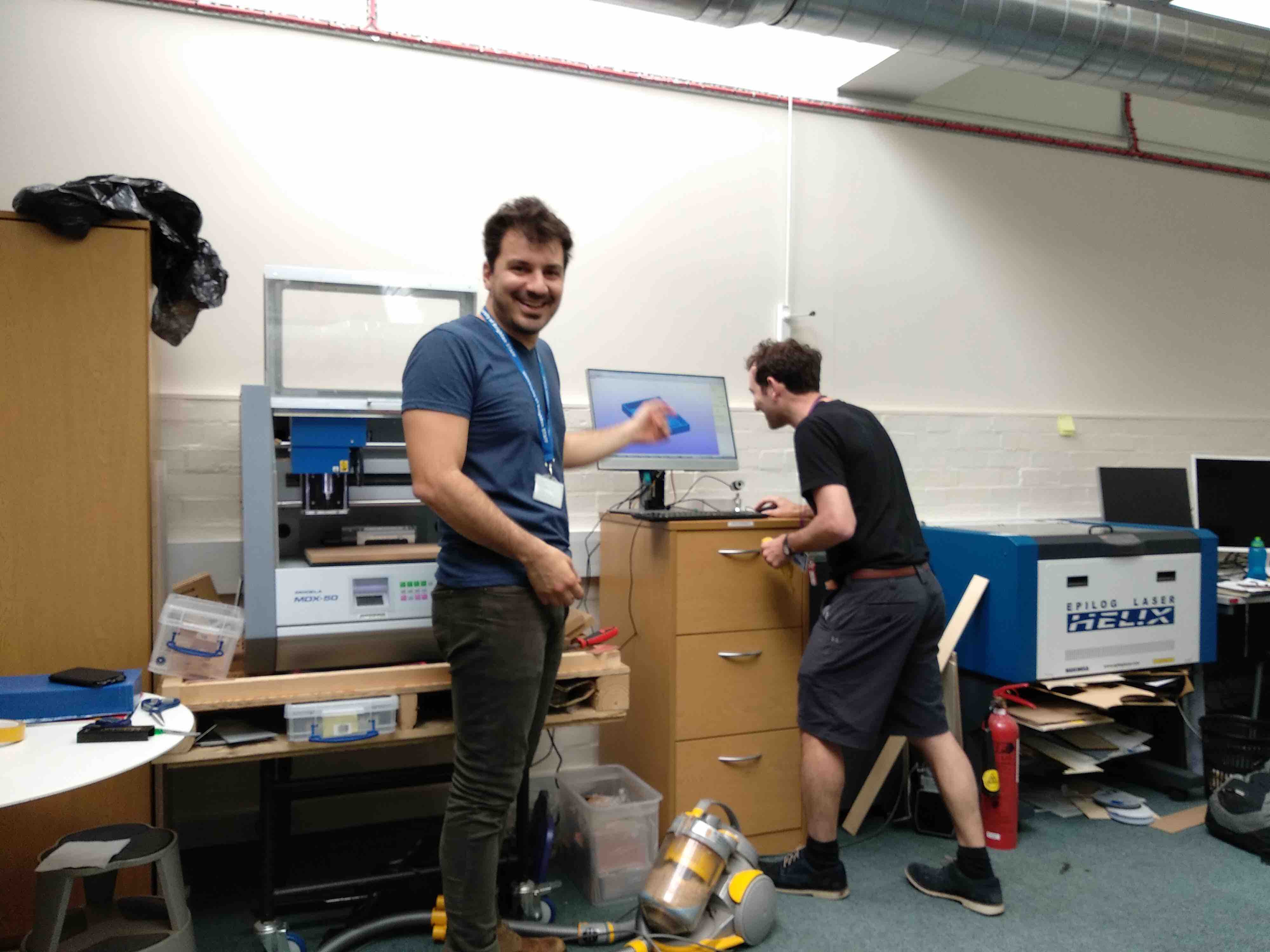
When the wax is milled, chips of wax flying from the milling bit in a fast rate, as the GIF above, but faster. At the end of job, all corners of the CNC machine are covered in a little hills of machinable wax's snow.
Not to waste all that good material, I laser-cut a 10x8x4cm MDF box using a 3.2mm thickness MDF sheet to serve as a mold, I'd then melt the wax's offcuts to then cast them back to machinable blocks. For the box design I used tabs of 3.2 mm lenght (it looks nicer when the tab is as long as the material's thickness).
In the Design lab across the hallway we have a big oven, max temp ~ 200 degrees Celsius. The melting point of the Machinable was is 116 degrees. Melted like butter. I've seen in other labs people using aluminium foil to coat the walls of the box. The wax sticks to the aluminium. What a mess! I wasn't sure what to expect from the contact of the molten wax with the MDF surface. Turned out that it just won't stick. As a result of the high shrinkage (between 5-10%), demolding was very easy. Another successful idea was to design a mold where the biggest side is the Z axis (hight). Once the block cools down, the top suffers deformations. Being the top a small area of the block, you could easily cut it down, or just ignore it and mill on the XZ or YZ surfaces.
This was first a test, proof of concept. Next round I'll gather all the wax chips in a big bag, bring it to accross the hall and melt it using a big cooking pan (that we don't yet have), and cast it into the, this time bigger, laser-cut MDF molds.
[#recycle #machinablewax #molding #casting #fabacademy #2018]
-KaLi closure
26th March - 1st April 2018
The last week of March was also the last week I got to keep my flat at the Wohnheim from the Studentenwerk Düsseldorf, located in Kamp-Lintfort (Germany), 1 minute walk from the University >Hochschule Rhein-Waal< from where I hold a Bachelor of Art's Degree in Communication Design. (To be honest, more a Digital Fabrication Communication's Design, since I explored Digital Manufacturing's techniques in most, if not all of my assignments throughout the course.) Despite the great memories I had in that place and the slight melancholic sensation to a chapter's closuse, I felt also an excitement and lightness of letting something go, when its time arrives.
It's Easter break in Fab Academy, perfect timming in all senses. I needed the break, now I reckon.
I come back with my batteries charged. To reencounter my KaLi friends was a great way to reflect upon what I am currently experiencing. Through their eyes, the perspective is fascinating.